Quality is life!
Our factory has a very strict quality control system at every production step !
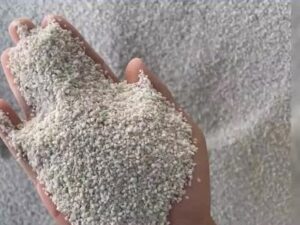
Raw material inspection during raw material selection.
Glass bottles are typically made from a combination of materials, including silica sand, sodium carbonate, limestone, dolomite, feldspar, and borax. Silica content is crucial for determining glass strength.

Batch House: Raw materials are continuously weighed, mixed, and transferred to the melting furnace. Magnetic materials are sometimes removed during this process.
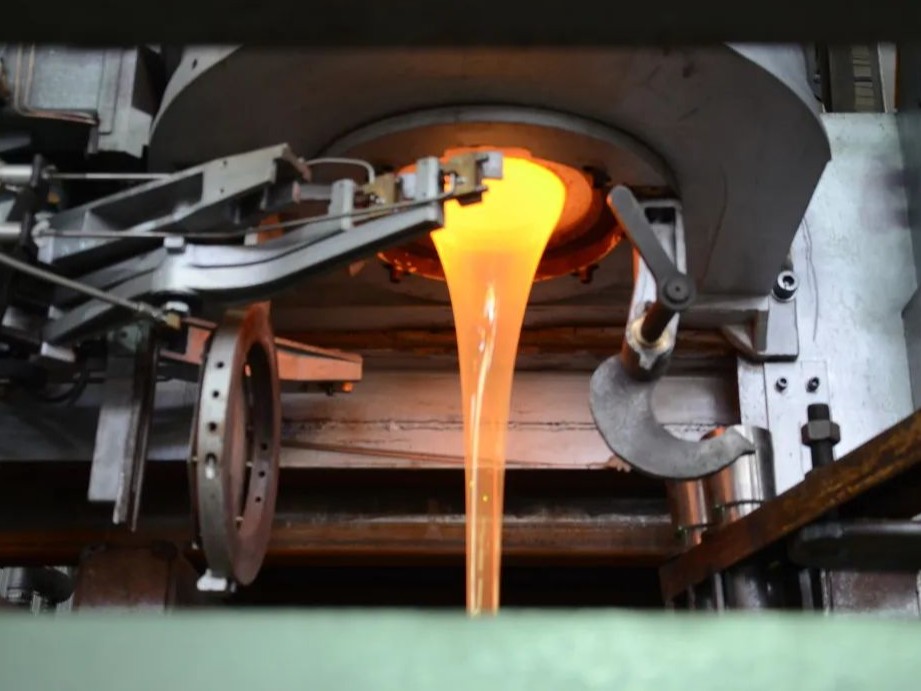
Melting: In the furnace, raw materials are heated to temperatures around 1550°C to 1600°C, forming uniform, bubble-free molten glass.
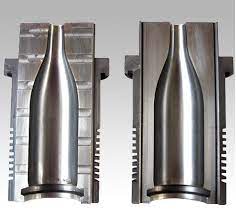
Mould checking to make sure the mould is not damaged and in best production condition .
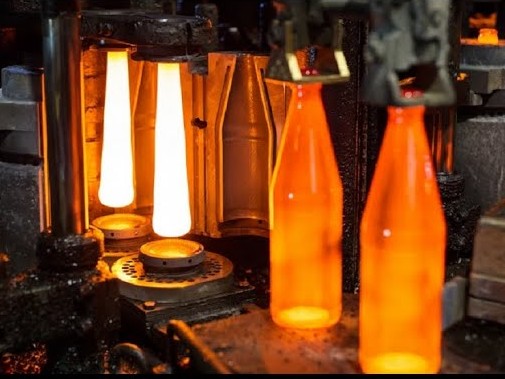
Feeding: The molten glass (gob) is fed into glass-bottle forming machines. The temperature is optimized based on bottle weight and shape.
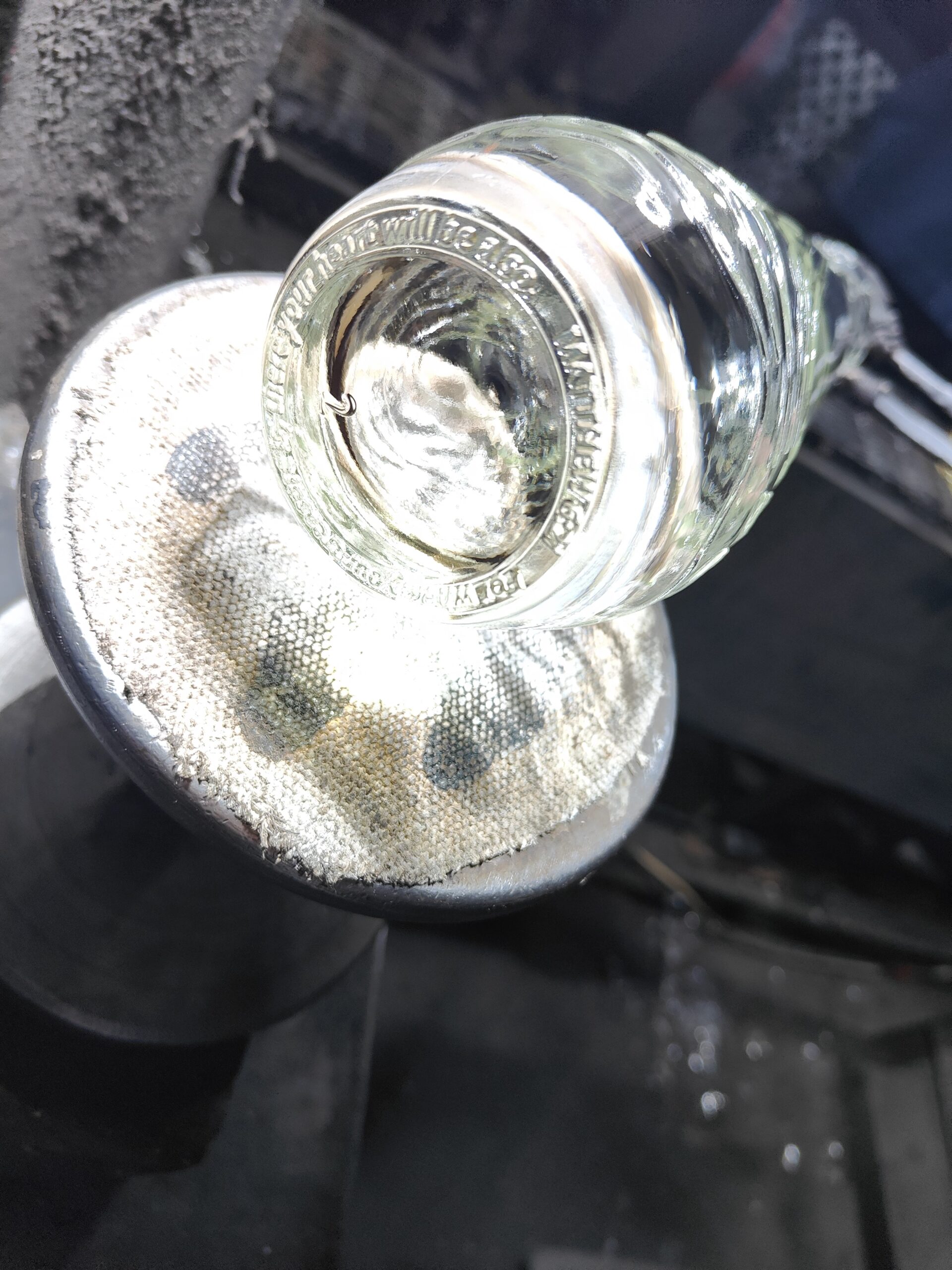
Quality checking during the production to make sure the bottles are good condition after 30-50 minutes’ production.Bottles undergo rigorous inspection for flaws and defects using both machines and human workers.

Cooling process ,all bottles come out from the mould will need cooling in a professional cooling tunnel .
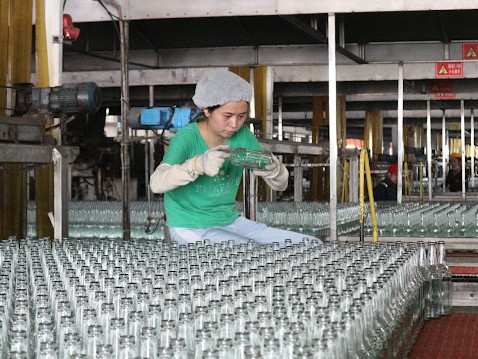
A quality checking process to make sure the bottles are not damaged before packed well !
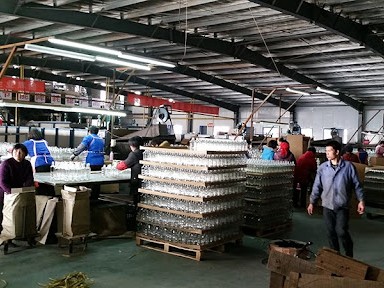
Packaging and Delivery: Glass bottles are carefully packed and shipped to customers using various methods.

Container condition checking .In order to make sure the glass bottles will not damaged during the transportation,we need check all to containers before loading ,to make sure the container is tidy and will not be infiltrated by water when on the sea .